Seven years ago, I discovered the art of weaving and was immediately drawn to the ability to create intricate, three-dimensional structures on the loom. My weaving classes taught me various techniques and materials that can be utilised to achieve this effect, and I was particularly fascinated by the idea of using multiple layers to create 3D textiles. As a product designer, this sparked my curiosity – could it be possible to weave an entire garment on the loom?
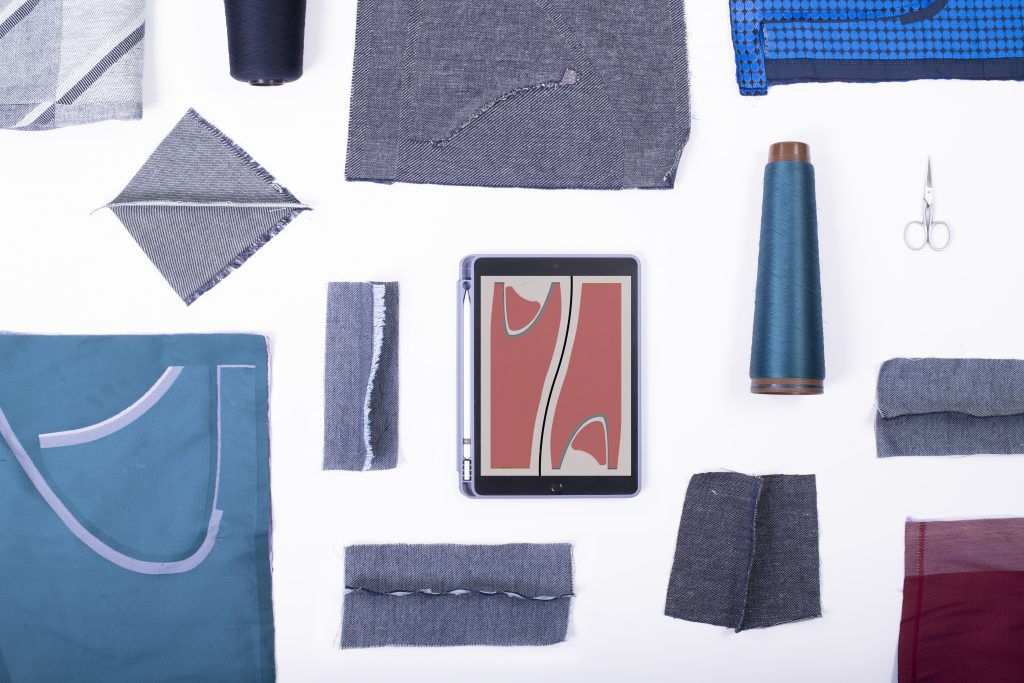
First steps in woven garment design
To fully explore the potential of weaving a complete garment on the loom, I knew I would need to collaborate with other designers to create innovative designs, work with industrial weaving mills to produce samples, and master the complex process of programming industrial jacquard looms myself. After dedicating several years to learning the intricacies of loom programming, I finally launched the project and created the first iteration of a woven garment – a pair of trousers.
For this project and many others that followed, I partnered with Holly McQuillan, a leading expert in zero-waste fashion design and currently an Assistant Professor at the Industrial Design Department of the TU Delft. Additionally, I collaborated with EE-labels, a Dutch weaving mill specialising in detailed fabrics and labels. Holly and I collaborated closely on this project, where she focused on designing the garments while I concentrated on developing the textile design. The garment designs were delivered as images by Holly, and using CAD/CAM software, I could assign the necessary weave structures to each colour.
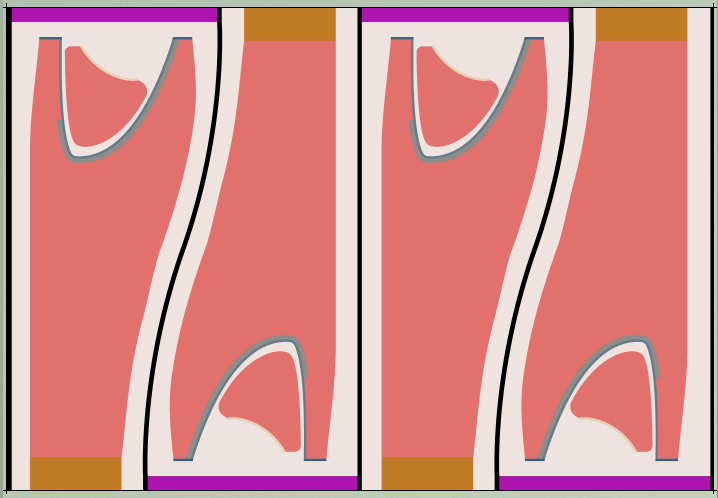
Right: This visualisation shows the density loss when fabrics are woven in multiple layers.
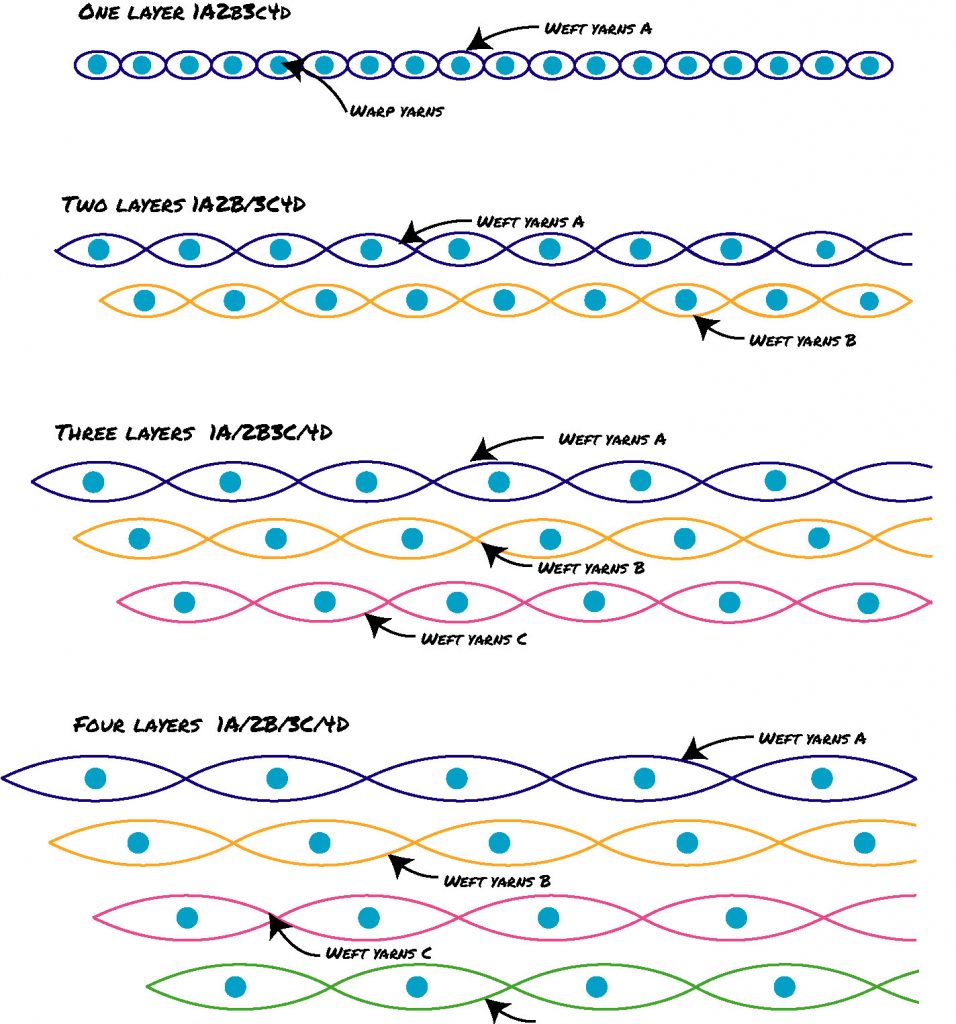
Multiple layers
The warp yarns, which are the yarns that are tensioned on the loom, play a crucial role in the weaving process. The warp yarns are either lifted or remain stationary, allowing the weft yarn to pass through. Weaving a garment on a loom requires the weaving of multiple layers. To weave these layers, a set of warp yarns is lifted so the yarns underneath can be woven. Jacquard looms, traditionally used for creating decorative patterns, can individually control each warp yarn, making it possible to separate and join the fabric according to the programmed weaving structures.
Although modern jacquard looms can weave in multiple layers, they are not designed to do it, and therefore, the more warp yarns there are, the thinner the fabric will be. While the number of warp yarns on the loom we used was relatively high, 78 warp ends per cm, the warp yarns needed to be split into four layers. The result is that the trouser will only have 19.5 warp end per layer. It can be incredibly time-consuming and therefore costly to change the material or setup of the loom due to the large amount of warp yarns (11520 in the case of the first trouser iteration). Therefore, we couldn’t change the material on the loom. To compensate for the loss in density, I decided to double the number of weft yarns inserted in the fabric.
Unfortunately, but not unexpectedly, the trousers’ first iteration was not without flaws. The fabric was too thin, the yarns were not arranged correctly, and the trousers were only partially finished due to dense woven bindings. Although imperfect, this first sample proved that it was possible to weave a garment on the loom, and I was eager to continue experimenting and iterating on it.
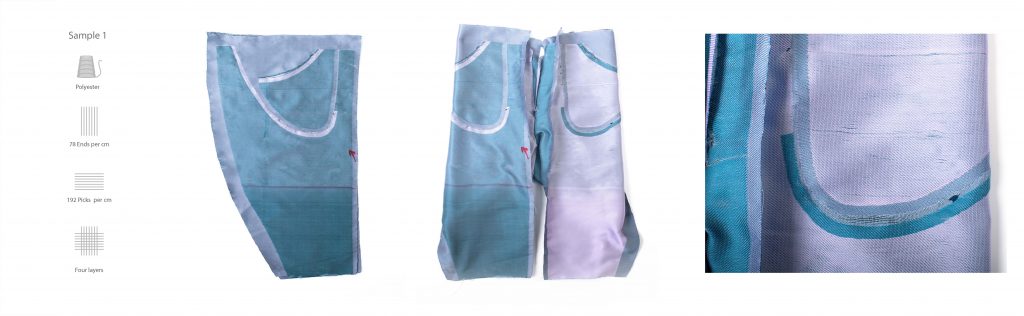
More than a technical question
This journey began with a technical interest, but as I delved deeper into my research, I realised the importance of considering the broader implications of my work in the fashion industry context. The Ellen McArthur Foundation, a charity dedicated to creating a circular economy, has reported that clothing production has nearly doubled in the last 15 years and that less than 1% of the materials used in clothing production are recycled (McArthur Foundation, 2017).
The current system of producing, distributing and using clothing is highly linear, with non-renewable resources being extracted to create clothes that are used for a short period of time. I believe my research into weaving garments on the loom can contribute to a more sustainable and circular economy. Holly describes in her doctoral thesis ways to integrate the garment construction process into the weaving process, with the aim of reducing the number of production steps and manual labour required in traditional cut-and-sew methods(McQuillan, 2019). This also allows for more localised production and, when designed well, could save the 15-20% of offcuts typically generated in traditional cut-and-sew methods
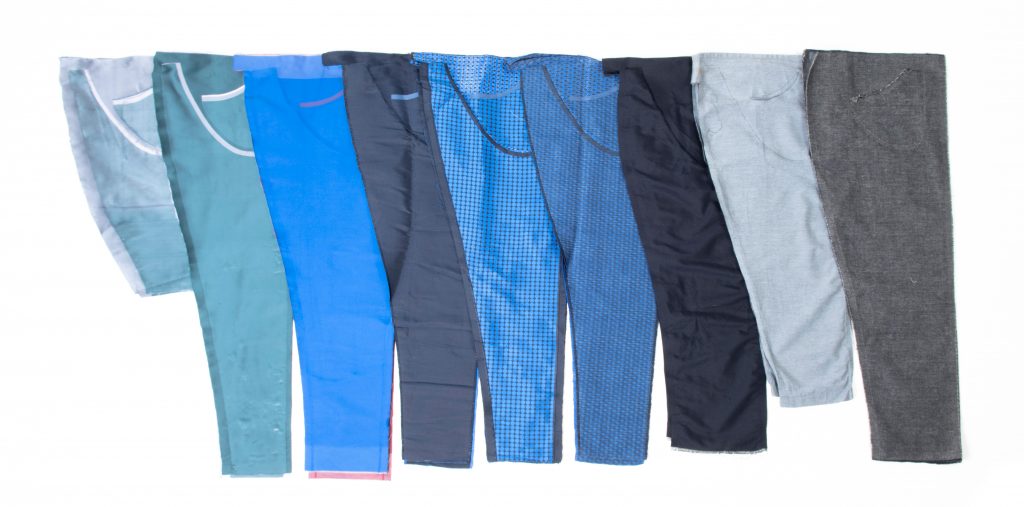
Many iterations
In the first iteration of the trouser, I discovered that the density of the fabric was a technical constraint I needed to overcome in my journey of weaving a garment on the loom. I initially wanted to design a garment made entirely out of one material, as blending materials in garments makes them, at best, difficult to recycle. The loom at the weaving mill was set up with a very fine polyester warp yarn; therefore, I chose to use a polyester weft (the yarn inserted in the loom) to create a mono-material garment.
While polyester had some benefits, such as being strong and durable, I also found many downsides. It is a non-renewable material and sheds microplastics when washed. Additionally, the yarn was slippery and combined with the low density, the fabric was not stable enough for a trouser.
In subsequent iterations, I attempted to address these issues through the use of functional patterns to increase yarn interlacement to create a more stable fabric. However, the resulting garment did not have the look and feel of a conventional garment.
My goal was to design a garment that could convince the industry to explore woven textile-forms as a potential future direction for garment making. To achieve this, I created an iteration using weft materials such as wool and recycled jeans yarns. Although it was not a big change, this was a breakthrough for me, as it finally felt like a real garment. I realised that while blending materials is not ideal, it is currently necessary due to the limitations of existing machines and processes. It reminded me that it is important to understand that the full body of work, not just the individual prototypes, will tell the story of this technique’s potential.
Working with the limitations
Last year, I had the amazing opportunity to continue my research project in collaboration with a denim-weaving mill in Pakistan. Working again with Holly, we used the same trouser design from the previous iterations. The mill had a different machine setup, with 40 warp ends per cm and indigo-dyed cotton. However, this weaving mill also presented a new challenge I had not encountered in my previous iterations, a jacquard repeat. This is a specific setup of the loom where some warp yarns are connected to the same jacquard hook, resulting in the same pattern appearing three times.
The uneven repeat size made it impossible to create a zero-waste garment. To overcome the low-density of the warp yarns, we chose to weave the trouser in two pieces, a left and right leg, which would then be stitched together We addressed both the repeat and density issue this issue though fitting one leg of the garment into the smallest repeat size, resulting in two pairs woven at the same time.
LEXICON
Woven textile-form.
Woven textile-forms, sometimes also named whole garment weaving or 3D weaving, are made through a design-production process that involves the simultaneous production of textile and form via the interlacement of yarns on the loom. The process is designed to facilitate localised, on-demand production of textile-based objects. This design process allows the (textile)designer control over two processes typically separated: textile production and form design.
As a textile designer, I often collaborate with different partners, often designers and weaving mills to produce woven textile-forms.
The potential of weaving
I believe that the textile and textile-form industry has the potential to become more sustainable, interactive, and innovative by utilising forgotten or almost-forgotten machines, methods, and techniques. By reframing these techniques and applying them in different contexts, we can tap into their potential and support the transition to a low-waste, circular economy.
The evolution of the industrial and craft sector has put traditional techniques at risk of disappearing, along with the valuable knowledge and skills of ancient techniques and materials. However, by combining these traditional techniques with modern technology, we can create new opportunities for innovative products and services that support the transition to a circular economy, preserving cultural heritage and the planet’s resources.
Changing aesthetics
As a designer, I understand that in order for textile products to respect the planet and people, we must rethink the way they are produced. The current textile industry prioritises efficiency and low costs, leading to poor working conditions, excessive use of raw materials, and waste. Therefore, in the transition to a circular economy, I believe that we should rethink our perceptions of aesthetics. When we strive to re-imagine systems, we should also reconsider our concepts of what a product should look like. As a designer, I am dedicated to exploring these evolving aesthetics while aspiring that the aesthetics of the garments I produce are the result of its sustainability goals and technical capabilities.
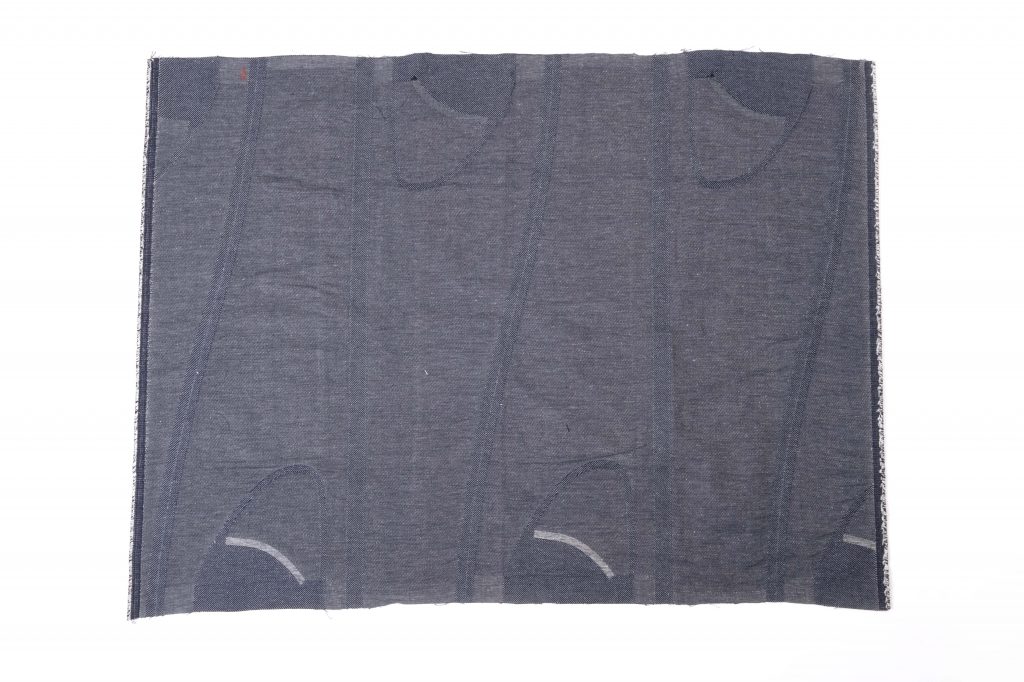
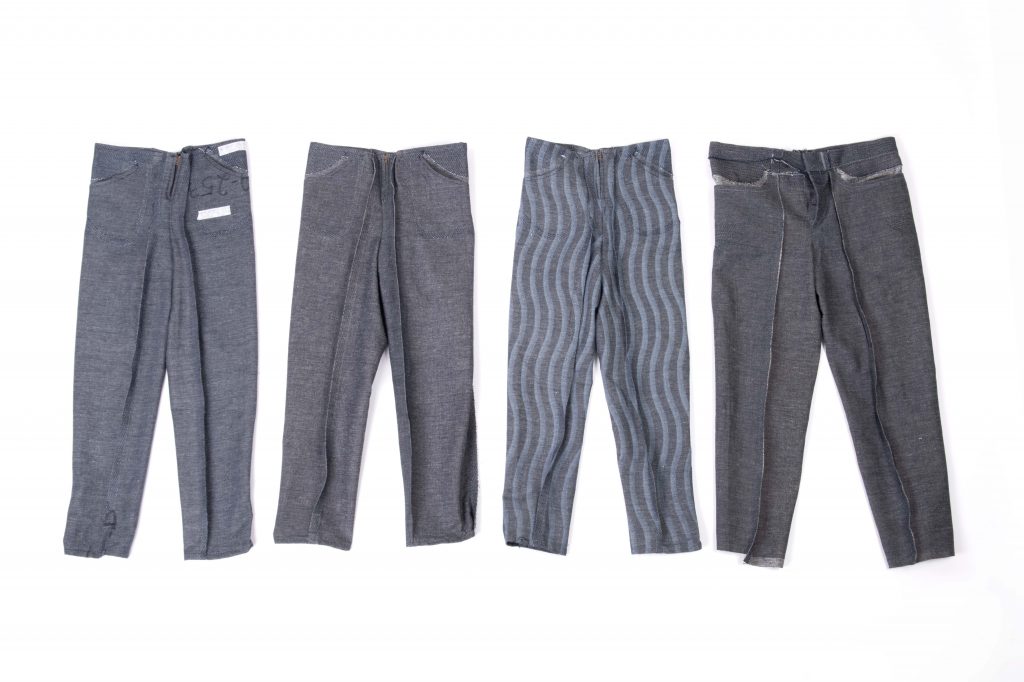
The fraying challenge
Another challenge I encountered throughout the process of designing garments on the loom was the tendency of the fabric to unravel when cut. To minimise the need for finishing steps after the weaving process, I aimed to design the garments so that the edges would not fray, however, this varies greatly depending on material weave structure and density of the fabric. Through my various iterations, I noticed that the amount of fraying varied significantly depending on the position of the cutting line. I found that straight edges frayed more heavily than angled edges, similar to the way pinking shears (saw -toothed scissors) work. The zig-zag pattern of pinking shears helps to prevent fraying by creating small notches that make it more difficult for threads to unravel.
In conclusion
My research on designing garments using the weaving technique on the loom has highlighted the need for a balance between sustainability, technical feasibility and aesthetic appeal. The current industrial setup of looms presents several constraints, including density, material limitations, width and repeat and fraying edges. Despite these challenges, it is possible to design garments on existing looms, however, it requires a shift in mindset and tweaking of machines to suit the process of woven textile-forms better. Additionally, the journey has led me to see opportunities in exploring historical weaving techniques as a way to solve these limitations, intending to utilise the full potential of woven textile-forms.
Sources
Ellen Mcarthur foundation (2017). A New Textiles Economy: Redesigning fashion’s future, ,https://emf.thirdlight.com/link/2axvc7eob8zx-za4ule/@/preview/1?o, page 18
McQuillan, H. (2019). Zero Waste Design Thinking (Licentiate dissertation, Högskolan i Borås)